Maximizing return on investment (ROI) is crucial for manufacturers. Zinc die casting’s extended tool life reduces replacement tooling costs in high-volume parts. This, in turn, leads to increased cost savings and improved productivity.
In this article, we explore the benefits of extended tool life in zinc die casting and the impact on your bottom line.
Enhance ROI with Extended Tool Life
When maximizing ROI in zinc die casting, one key factor that directly impacts profitability is extended tool life.
When you have high-run parts, you can reduce tool replacement frequency. Zinc alloy molds last ten times longer than aluminum molds.
Which reduces costs associated with purchasing new tools and Production Part Approval Process costs.
Additionally, extended tool life increases productivity. Allowing to maintain the production process without interruptions for periods to replace the tool.
When a tool becomes excessively worn, it affects the quality of the part. Worn tools can lead to defects such as increased flash and other imperfections in diecast parts.
With extended tool life, we can achieve higher-quality castings. Over time, the tools maintain their precision and integrity. Therefore, reduced scrap rates and rework.
FAQ: Extended Tool Life in Zinc Die Casting
How does extended tool life impact profitability?
Extended tool life directly influences profitability by reducing replacement costs and maintaining uninterrupted production.
What are the benefits of minimizing tool wear?
Minimizing tooling wear through effective die management practices extends tool longevity but also minimizes production interruptions, leading to higher productivity levels.
What role does zinc’s lower abrasiveness play in enhancing tool life?
Zinc’s lower abrasiveness is a key factor in enhancing tool life. It results in better bearing surfaces upon solidification, reducing tool steel erosion and significantly improving overall tool longevity.
How does zinc’s melting temperature contribute to extended tool performance?
Zinc’s lower melting temperature, ranging from 780 to 800 degrees Fahrenheit. Compared to aluminum’s 1,200 degrees Fahrenheit, it plays a crucial role in reducing thermal stress. This not only contributes to less mold erosion. But also enhances tool performance, including features such as slides and ejection mechanisms.
Comparing Zinc Tool Life with Other Metals
When considering zinc’s tool life in comparison to other metals, you might be curious about its performance. Zinc’s significant advantage, especially in casting applications, lies in its distinct properties.
1. Lower abrasiveness
Zinc Alloys vs. Aluminum: Zinc alloys exhibit lower abrasiveness. This characteristic not only allows for better bearing surfaces when solidified but also results in less tool steel erosion. Zinc alloys offer significantly improved tool life.
2. The melting temperature.
Aluminum Comparison: Aluminum has a melting temperature of around 1,200 degrees Fahrenheit.
Zinc’s Melting Temperature: In contrast, zinc’s preheating temperature ranges from 780 to 800 degrees Fahrenheit. With a melting temperature around 722 degrees Fahrenheit (varying slightly depending on the alloy).
The lower melting temperature reduces thermal stress, contributing to less mold erosion. As well as enhanced tool performance, including features such as slides and ejection mechanisms.
3. Extended Die Life
Zinc’s Advantage: Zinc has a longer tool life because it is less prone to erosion. Typically zinc die-cast mold yields approximately a million shots, and in exceptional cases it has exceeded three million.
Aluminum Mold Comparison: By comparison, aluminum mold may achieve only 10% of the same life. Resulting in significant variations in tooling costs and production longevity.
Leveraging zinc’s properties—lower abrasiveness, optimal melting temperatures, and extended die life—can lead to substantial cost savings. As well as increased efficiency in the production process.
Zinc Alloys for High-Volume Castings
In relation to high-volume casting, zinc alloys can offer a range of benefits. Zinc alloys have excellent fluidity, allowing easy casting into intricate shapes with tight tolerances.
This allows die casters to produce complex components with minimal post-processing or machining requirements, saving time and resources.
Furthermore, zinc alloys have exceptional corrosion resistance, ensuring casting longevity and durability. Additionally, zinc alloys’ low melting point allows for energy-efficient casting processes. This, combined with their recyclability, makes zinc alloys a sustainable choice for high-volume castings.
Overall, zinc alloys for high-volume castings maximize ROI by reducing production costs and ensuring high-quality, durable parts.
Highlight The Benefits of Extended Tool Life
- Increased production rates
- Improved part quality and consistency
- Cost savings on tool maintenance and replacement
- Reduced downtime and production interruptions
- Longer tool life and extended investment
- Enhancing overall efficiency and profitability
In conclusion
We have seen the benefits of extended tool life in zinc die casting.
From cost savings to increased efficiency and improved quality, the ROI advantages are clear.
By implementing methods to extend tool life, we can achieve these goals. Deco Products utilizes innovative zinc die-casting techniques to drive business success and growth.
Capabilities and Services
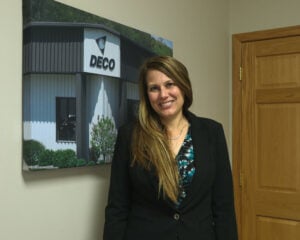
Michele Duwe
Michele Duwe is the Sales and Marketing Manager with Deco Products. She has eight plus years as a digital marketing manager and over a decade of sales and marketing experience.