Engineers rely on die cast zinc for a reason: strength, precision, and efficiency. At Deco Products, we work with zinc every day. We’ve seen how well it performs in many demanding applications. Whether you’re designing a part that needs high impact strength or fine tolerances, zinc delivers.
As a zinc die caster, we key love educating our customers about zinc alloys. Our engineers are always available to discuss what makes zinc an excellent material for die casting.
Built to Handle Stress and Wear
Manufacturers recognize die cast zinc for its mechanical strength, impact resistance, and wear resistance. Zinc alloys stand up to force, vibration, and daily use. That’s why zinc components are common in parts like locks, brackets, and housings.
Zinc’s impact strength makes it a strong candidate when your part needs to absorb shock. Some zinc die casting alloys reach tensile strengths of up to 54,000 psi. Impact resistance is the primary performance characteristic that separates zinc from aluminum castings.
Zinc alloys provide high yield strength, ensuring parts maintain structural integrity under load.
Precision Without Extra Machining
Zinc’s high fluidity allows it to fill intricate mold cavities with precision. This allows engineers to design products with thinner walls, finer details, and integrated features like ribs or logos without compromising strength.
Since zinc can be cast with greater precision, many features can be cast in to the product, which otherwise would have required machining with another material. This allows castings to be produced with fewer operations and lower total cost to the end customer.
Dave Magner, our Director of Sales and Marketing at Deco Products was interviewed on Small Business Talks podcast where he discussed these advantages:
“A characteristic of Zinc is it’s very fluid and so when you melt it, the fluidity is quite high. And it melts and it flows like water, where other metals are more syrupy and don’t flow quite as well. You can design precision features, small thin walls, specific radiuses that are important to one’s design.”
Listen to the full podcast interview: Zinc Die Casting in Manufacturing.
Long Tool Life
A major advantage of zinc die casting is longer tool life. Zinc melts at a much lower temperature than most other metals used in casting.
Zinc alloys melt between 700°F and 800°F. These melting points are much lower than aluminum alloys, which melt closer to 1,200°F. Lower temperatures of zinc casting result in slower wear on the steel tooling and fewer thermal stresses during casting.
This translates into much longer tooling life: zinc die casting tools can run well over a million shots. With proper design and maintenance, we’ve seen tools exceed three million cycles before they needed to be replaced. Fewer tool changes and less downtime mean consistent part quality and lower total cost.
Surface Finish That Works
Thanks to the fluidity of zinc, the die castings typically come out of the mold with a smooth surface. This gives the parts an attractive quality look and generally makes it easier to apply decorative finishes, such as powder coating or plating.
Many of our customers take advantage of our in-house powder-coat service Powder Coating: Deco’s Powder Coating Capabilities. However, we also have a large number of customers who prefer to keep zinc with a raw cast finish.
These customers can buy the zinc with a raw finish because zinc alloy naturally resists corrosion. When exposed to air, zinc forms a protective patina that stabilizes the oxidation of the zinc. Regardless of your application, zinc can be a great solution for function and appearance.
Want more information how zinc alloys exhibit corrosion resistance? Read our article on why zinc is a good corrosion-resistant metal.
Environmentally and Economically Sound
Zinc is essentially 100% recyclable without losing strength or performance. Manufacturers use recycled zinc again and again in die casting operations. That makes zinc a responsible choice for sustainability.
The number one use of energy in the typical diecasting company is generating heat to melt the alloy into a castable liquid. The lower melting temperature of zinc also means it takes much less energy to process. This helps reduce emissions and utility costs during die casting production.
If your team is factoring in environmental impact, zinc alloys help meet those goals without trade-off
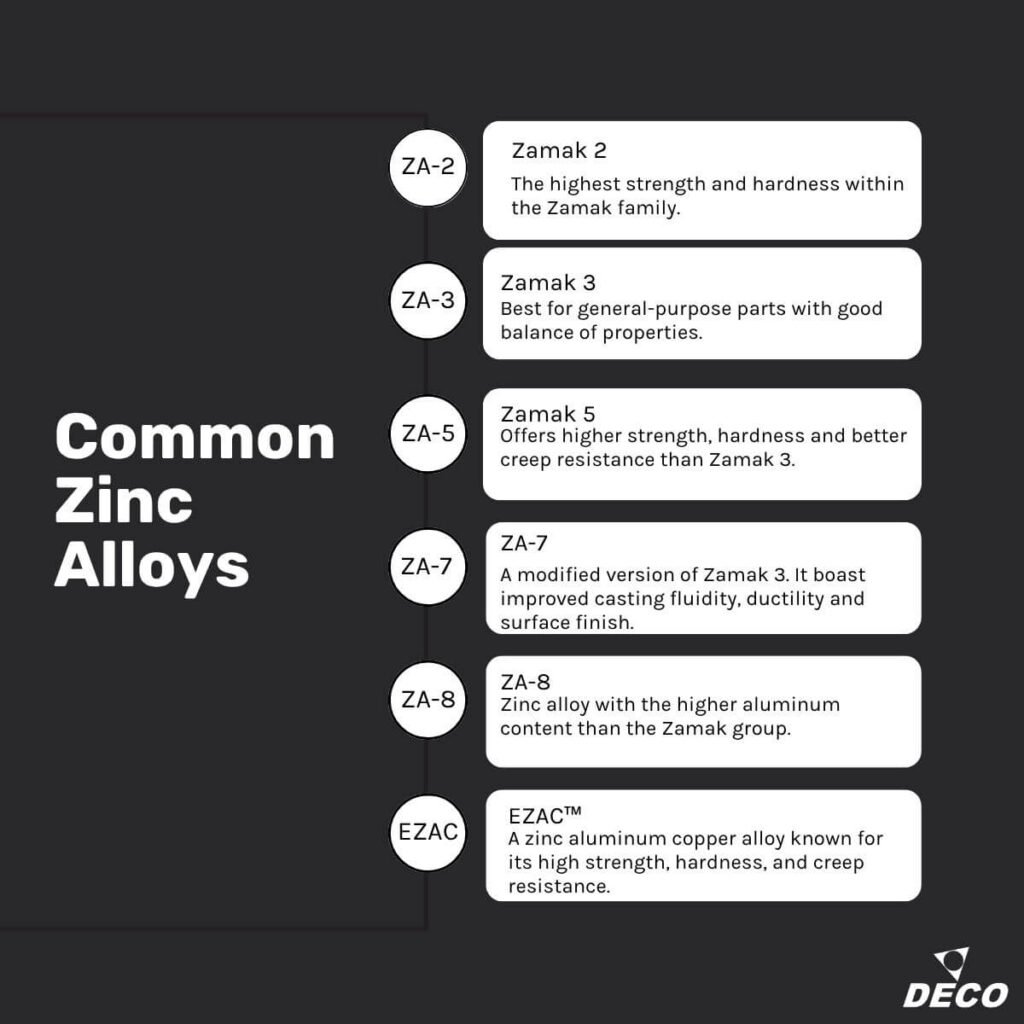
Common Zinc Alloys and Where to Use Them
ZAMAK 3 is the most used zinc alloy used to cast parts in North America. It offers a strong balance of performance, fluidity, and dimensional stability. If you’re looking for durability in a high-volume part, this is a good place to start.
Zinc alloys vary by strength, castability, and resistance to wear or creep. Here are a few common options:
- ZAMAK 3 – Best for general-purpose parts with good balance of properties.
- ZAMAK 5 – Adds copper for increased strength and hardness.
- ZAMAK 7 – Improved fluidity and surface finish for complex parts.
- ZAMAK 2 – Strongest ZAMAK in as-cast form, with higher hardness.
- ZA-8 – Better for high-load or elevated temperature applications.
- EZAC™ – High-performance option with excellent creep resistance.
Choosing the right alloy depends on your design goals. But in most cases, ZAMAK 3 is often the most economical and the standard choice for projects.
When Zinc Is the Right Fit
Zinc makes sense for designs that require detail, durability, and volume. Consider zinc if your part fits into one or more of these buckets:
- Production runs over 50,000 units – Tooling lasts, cost per part drops.
- Tight tolerances or fine features – Precision casting avoids extra machining.
- Parts exposed to impact – Strong and rigid for structural applications
- Visible parts – Smooth finish and excellent coating compatibility.
- Harsh use or environments – Natural corrosion resistance extends life.
Final Thoughts
Die cast zinc combines strength, precision, and process efficiency. Its mechanical properties, corrosion resistance, and recyclability make it a standout choice in die casting materials.
At Deco Products, we help customers choose the right alloy, optimize part design, and deliver quality castings at scale. If you’re designing metal parts for strength and precision—and want a partner who understands die casting processes—we’re ready to help.