In High Pressure Die Casting (HPDC), gate runner sprue design helps the quality and functionality of the final product. A typical zinc die casting gate design includes the sprue, runner system, gate, overflows, and vents. Each element of the sprue runner and gate system controls material flow and part integrity.
What Is Degating in Die Casting?
During casting, the molten zinc enters the mold via the gate. Once the casting solidifies, you must remove the gate. This process is called degating.
Degating removes excess material from the cast part. Proper gate sizing ensures smooth molten material flow. It reduces pressure loss and helps cleanly break the gate from the part.
Gate design affects strength, surface finish, and cost. Understanding the zinc die casting gate system is key to producing high-performance parts.
Gating in Zinc Casting
Gate design is one of the most critical issues of trying to fill die cast parts. The injection molding machine injects molten zinc through the gate into the mold.
The gate runner allows metal to flow smoothly and fill the mold with precision. The design and placement of these gates are essential to achieving optimal casting results.
Design engineers place gates to reduce turbulence and minimize air entrapment. Gate location also affects flow rate and casting quality.
Larger gates improve material flow but may reduce surface finish. Small gates reduce material but can increase defects. Engineers balance these traits for each casting.
Gate location and geometry also influence cycle time, material waste, and the need for secondary machining.
Common Zinc Die Casting Gate Styles
At Deco Products, we use several zinc die casting gate designs:
- Tangential gates
- Chisel gates
- Fan gate systems
- Modified Australian gating systems
The different styles of gates help to deliver the flow to the casting the way we want.
The choice of gating system design plays a crucial role in the overall casting process. Engineers commonly use a variety of gates, with each gate serving a specific purpose.
To look at different gating styles, Deco’s engineering team will run simulations using finite element analysis software. By running simulations, it allows us to see the intricacies of gating designs for our customers.
Role of the Sprue and Runner System
The sprue channels molten zinc from the crucible to the main runner. The runner system connects to secondary runners, distributing metal to each multi cavity mold.
A sprue bushing helps center the sprue and control metal entry. These elements reduce pressure loss and balance flow through the casting.
Edge gates help fill wide or flat parts, reducing warping. Proper gating avoids hot spots and material segregation.
Additionally, the fan gate allows for optimal flow and minimizes turbulence, making it suitable for complex geometries.
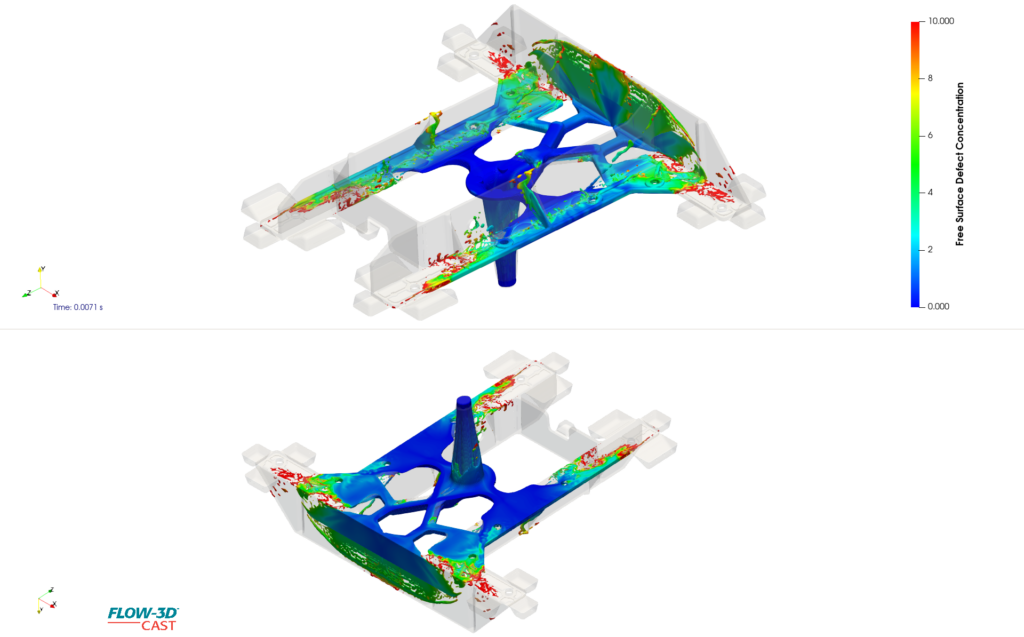
Overflow and Air Control
Another strategic location is where we put the overflows. The purpose of an overflow is to draw any air entrapment and air entrainment out of the casting.
Poorly placed gates or missing overflows can trap air. This leads to surface blisters and structural weaknesses. Engineers place these based on flow simulations to reduce porosity and voids.
Simulation-Driven Gating Success
The flow simulation helps verify the gate design with zinc castings. Our engineers are able to try different types of processes to use when designing a casting.
Using flow simulation allows us to get radical with our designs. Jim Myers, Senior Engineer, recalls, a large casting they designed with help of flow simulation. The casting was a foot for the underneath component of a table.
Jim said, “I went with a bizarre what we call caliber gates, where we have two tangential gates approaching each other.”
All the flow comes in the middle and collides when using the two tangential gates. Two gates caused the molten zinc to come in the center. The flow simulation showed the zinc start filling the cavity and pushed the air out of the casting that way.
Typically, when you glide flow, it does not have a good outcome. The simulated parts looked good, leading us to build the tool that way. This is a radical concept, to fill it in the center and have the flow keep building and push the air out. With flow simulation they were able to try it using a color scale to visually show where the defect will occur at.
Cost Facture in Gate Location
Another factor to consider with a quality part is part geometry and wall thicknesses. We use different styles of overflow to make sure that the gasses, once we pull them out of the casting, don’t reenter the casting. Jim, uses that example, illustrating how the geometry of a part can trap air during the fill.
Jim continues with a lot of times the customer has restrictions on what they’re calling decorative surfaces. They will not want a gate location in a certain area. That adds a lot of complications then perhaps with the geometry of the part.
When we are unable to put a gate where it needs to be, the part will need to go through a machining operation. This secondary machining may be a buff operation, trying to eliminate the gate presence as much as possible.
The gate location can play a part in cost effectiveness of the casting. Added machining operation will increase the cost of the casting.
Machine Selection Factors in Gate Design
To get better quality parts we use large tonnage machines. However, when part price takes a higher priority than quality, we design the casting with multiple cavities.
Using multiple cavities for the casting, provides a reduction of cost. Our design engineers provide the best quality mechanical finish or paint finish they can achieve with multiple cavity castings. However, it is sometimes difficult to obtain a cast with this design for paint finish and plate finish.
Zinc Degating Methods
Common degating methods include:
- Sawing – Cuts off thick gates.
- Grinding – Smooths excess material, good for complex shapes.
- Thermal methods – Use flame or torch to melt off gates.
Each method fits different needs depending on part size, material, and finish requirements.
Vibratory Degating at Deco
We also offer vibratory degating at Deco Products. This uses vibration to remove gates, runners, and sprues. Vibratory degating is one of the value-add process that we offer at Deco Products.

The Process to Remove the Gate
Skilled technicians use techniques to remove the gate without compromising the structural integrity or accuracy of the casted part.
The goal of degating is to achieve a superior finish on the final zinc die-cast product. This involves careful removal of the gate to meet the desired specifications. Efficient degating minimizes the need for additional finishing processes, contributing to the overall efficiency of the zinc die-casting operation.
Similar to gating, the degating process undergoes continuous improvement. Deco Products uses its expertise and stays updated on technology to improve degating techniques and product quality.
Importance of Gate and Degating Design
Gate and degating design influence casting performance. Poor design can lead to trapped gas, surface defects, and added costs.
Deco uses simulations, experience, and customer feedback to refine gate location, size, and geometry. Our goal is simple—smooth flow, strong structure, minimal defects.
We customize gating systems based on casting needs. Contact the Engineering Design experts at Deco Products.
Our Design Team's Expertise
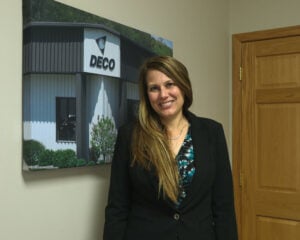
Michele Duwe
Michele Duwe is the Sales and Marketing Manager with Deco Products. She has eight plus years as a digital marketing manager and over a decade of sales and marketing experience.