
In high-pressure zinc die casting, degating refers to the process of removing the excess material. This excess material has different components such as the runner, the over-flows, or the gate.
In this article, we will discuss the importance of degating in zinc die casting. In addition, how it affects the final quality, surface finish, and overall production cost.
Overview of Zinc Die Casting Gates
The degating process in zinc casting plays a crucial role in ensuring the quality and functionality of the part. These gates serve as the entry points for the molten metal, allowing it to flow smoothly and fill the mold with precision. The design and placement of these gates are essential to achieving optimal casting results. The strategic positioning of gates minimizes the fluid turbulence, reduces the risk of air entrapment, and overall facilitates optimal molten metal flow. The size and shape of the gates impact the efficiency of the casting process whereas it impacts the production cycle time and material usage. Overall, a well-designed system of zinc die casting gates is vital for achieving high-quality, defect-free castings.Types of Gates Used
In zinc castings, the choice of gate design plays a crucial role in the overall casting process. Manufacturers commonly use a variety of gates, with each gate serving a specific purpose. The sprue gate is one type that transfers molten metal from the crucible to the mold cavity. This gate design allows for a controlled and smooth flow of metal, ensuring uniform filling of the mold. Another common type is the runner gate, which connects the sprue to the individual cavities in multi-cavity molds. It helps distribute the molten metal evenly, reducing the chance of defects such as porosity. Additionally, the fan gate design allows for optimal flow and minimizes turbulence, making it suitable for complex geometries. Each of these gate types offers advantages, selecting the appropriate gate design is essential for achieving high-quality and defect-free zinc castings.Types of Processes Used to Degate a Zinc Part
You can employ various processes to successfully remove the excess material, or “degate,” from a zinc part after casting.
A very basic way to degate a part is to remove the excess material by hand degating. This could be done for a light small part that runs in lower quantity runs and so automation is not as feasible.
Trimming uses specific tools called a trim die and a press to shear the excess material. This process is suitable for higher running parts and could be performed by hand or robotically.
Another technique, called sawing, where a specialized saw cuts through the extra material. This approach is effective for parts with thicker gates.
Lastly, a very important degating method is vibratory degating. This process vibrates the parts and excess materials and breaks them apart and then separates the good parts from the excess material. This process is very efficient and allows the large quantities of parts to be processed in an automated way.
These processes offer different advantages. You may select processes based on factors such as part complexity, desired quality, size, and/or quantity of parts being run. By considering these diverse techniques, manufacturers can effectively degate zinc parts to meet the expectations for a high value solution.

Conclusion
In conclusion, gates play a crucial role in the overall casting process and the quality of the final product. By understanding the types of gates and degating processes, manufacturers can make informed decisions to achieve the desired results.
Whether degating by hand or with very expensive robotic equipment, proper degating is essential for a smooth and efficient production process.
With the right knowledge and techniques, zinc die casting can continue to be a reliable and cost-effective method for creating durable and high-quality parts.
Advantages of Zinc Die Casting Process for Deco Products
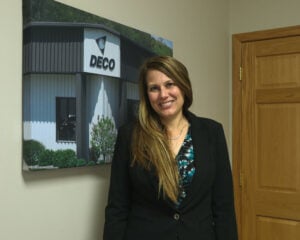
Michele Duwe
Michele Duwe is the Sales and Marketing Manager with Deco Products. She has eight plus years as a digital marketing manager and over a decade of sales and marketing experience.