Advantages of Zinc Die Casting Process for Deco Products
Zinc die casting is a widely used process in the manufacturing industry due to its ability to produce high-quality parts with intricate designs at a relatively low cost. Understanding the zinc die casting process can help you make informed decisions when sourcing parts for your company. We will explain the basic steps involved in the zinc die casting process, from designing the mold to casting the part, and finishing the product.
Designing the Mold
The first step in the zinc die casting process is designing the mold. A well-designed mold is crucial in achieving a high-quality part. Factors to consider when designing a mold include part complexity, material flow, and parting line.
There are various tools and software available for mold design. Deco Products engineers have extensive expertise to assist you with the design process.
Preparing the Zinc Alloy
Once the mold design is finalized, the next step is preparing the zinc alloy. Zinc alloy is mostly composed of zinc, but the alloy has other elements such as aluminum and copper to improve its excellent casting properties.
The preparation process involves melting the alloy. Deco Products only uses certified alloys which ensures that the material chemistry meets required specifications. Then it is important to monitor the melted alloy. Controlling the alloy temperature and composition is critical in achieving a high-quality casting.
Casting the Part
The casting process involves clamping the mold, injecting the molten alloy, and cooling the part. Controlling the process parameters such as injection speed, pressure, and temperature is crucial in producing a defect-free part.
Common defects in zinc die casting include porosity, shrinkage, and flash. Deco
Products utilizes process control sensors in their systems and mold flow simulation software to give engineers unprecedented insight into what happens inside the mold.
With Flow3D-Cast software, Deco engineers can simulate the process and examine the metal flow patterns, pressures, temperatures, and velocity.
This technology is an essential tool for Deco, allowing us to produce high-quality die cast products with minimal defeats.
Finishing the Product
The final step in the zinc die casting process is finishing the product. Post-casting processes could include trimming, degating, tumbling, thermal deburring, polishing, buffing, machining, and surface finishing.
Parts can be provided raw, but at times, finishing is essential for the performance and aesthetics of the part. Common finishing techniques include powder coat painting and plating, either decorative (e.g., chrome, brass) or functional (e.g., zinc chromate). The choice of finishing technique depends on the application of the part.
Conclusion
In conclusion, understanding the zinc die casting process is crucial when sourcing parts for your company. A well-designed mold, controlled alloy composition and temperature, and a defect-free casting process are essential in achieving a high-quality part.
Deco Products has the expertise to guide you through the entire process and provide you with a part that meets your specifications. We hope this has been helpful to you in understanding the zinc die casting process.
Zinc Die Casting Services
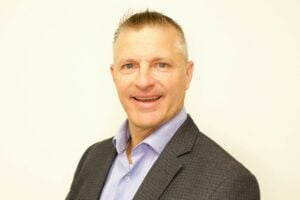
Dave Magner
Dave Magner is the Director of Sales and Marketing and has been with Deco Products since 2015. He has a +20 years of engineering experience in mechanical and electrical testing and design and zinc die casting, plastic injection molding, stamping, assembly, and automation processes.