In manufacturing, especially in zinc alloy casting, die casting molds are essential for producing high-quality parts. These die casting molds are made of hardened steel and engineered to endure the intense heat and pressure during the casting process. As such, to produce high-quality zinc alloy castings, die casting molds are crucial, and attention is needed in the design and fabrication of this tooling.
Die Casting Process
Die casting is a high-volume manufacturing process that produces intricate parts with minimal post-processing. It involves injecting molten zinc into custom tools with die cast die cavities at high pressures.
As the molten zinc cools and solidifies, it takes on the exact shape and features of the mold. Often, without further secondary operations, the “as cast” part is complete with the critical attributes of the design intact.
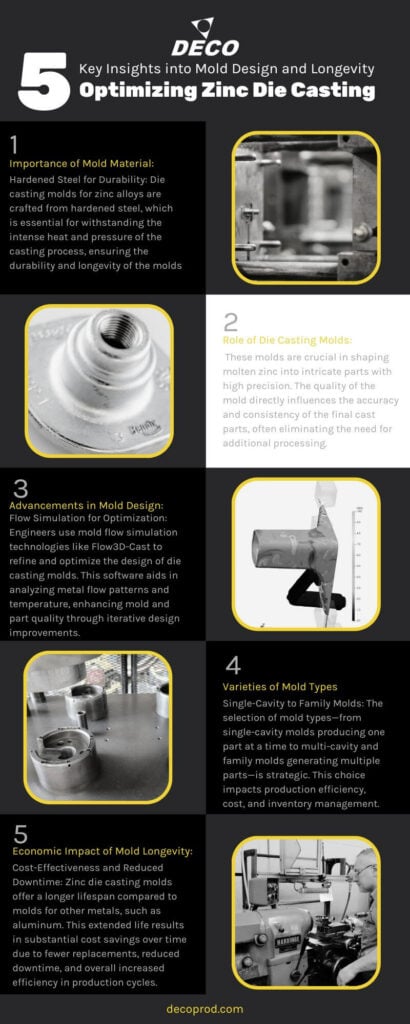
Die Casting Molds
Engineers innovate with designs of die casting molds that utilize mold flow simulation. This allows for increased optimization with an iterative design approach to ensure high part quality and tool life—resulting in immediate and long-term savings.
Mold flow simulation enables the examination of metal flow patterns, velocity, temperature, and pressure. It identifies areas of risk and improvement so that subsequent designs and simulations can be improved.
Deco uses a software called Flow3D-Cast allows design engineers to simulate the entire casting process. This software is especially suited for examining molten metal and is an industry leading software for zinc die casting engineering.
Types of Die Cast Dies
An important design consideration is the type of zinc die casting molds best suited for the part design. A factor that engineers consider is the number of cavities in a die. This is important as it affects the overall cost of the mold.
Single-Cavity Dies: The most common is the single cavity die, used to produce one part at a time.
Multi-Cavity Dies: These dies can produce multiple parts in a single die.
Family Molds: These specialized dies produce multiple different parts in one cycle. Ensuring balanced inventories of parts typically used together. These molds can include sliding mechanisms or cores to create complex features such as holes in the parts.
Longevity and Cost-Effectiveness
Zinc die casting molds have a significantly longer lifespan compared to molds used for other metals such as aluminum. Molds have a longer lifespan; they can last up to ten times longer. Because of the lower melting point and less abrasive nature of zinc alloys.
In die casting, tool life can impact the bottom line for manufacturers. Molds not properly designed or maintained increase the potential risk of part scrap causing higher cost and lower mold life.
Replacing die casting molds frequently causes a financial burden on manufacturers. Along with the extra works required for the approval of new tooling plans and part approval.
Therefore, the extended die life translates into substantial cost savings over the product lifecycle. Manufacturers benefit from reduced downtime and fewer mold replacements. Making zinc die casting a cost-effective choice for high-volume manufacture parts.
Visit This Post: Maximizing Success in Zinc Die Cast Design – Deco Products
Conclusion
Proper die cast mold design is essential for achieving high-quality zinc alloy castings. The innovation used with mold flow simulation and its advanced design techniques ensures the molds are optimized for performance and longevity.
Zinc die casting molds offer exceptional durability and cost savings, making them a smart choice for high-volume manufacturing. By leveraging these advancements, manufacturers can produce intricate and reliable parts efficiently, securing a competitive edge in the market.
Discover how Deco Product can help you maximize your die casting success with our expert solution and innovative technology Explore our services to take your manufacturing process to the next level.
Frequently Asked Questions
1. What makes zinc die casting molds more durable than those used for other metals?
Zinc dies casting molds have a significantly longer lifespan compared to molds used for other metals, such as aluminum. This durability is because of the lower melting point and less abrasive nature of zinc alloys.
These factors reduce wear on the molds, allowing them to last up to ten times longer. This extended die life translates into substantial cost savings over the product lifecycle. Making zinc die casting a cost-effective choice for high-volume manufacturing.
2. How does mold flow simulation improve the design and efficiency of die casting molds?
Mold flow simulation is an essential tool for designing efficient die casting molds. By simulating the flow of molten zinc within the mold cavity, engineers can predict potential issues such as air entrapment, incomplete filling, and temperature variations.
This process allows for multiple iterations of mold design. Allowing engineers to optimize the placement of gates, runners, and vents to ensure uniform filling and solidification. Using software like Flow3D-Cast, engineers can anticipate and resolve issues during the design stage, improving overall mold performance and part quality.
3. What are the different types of die casting molds, and how do they affect production?
Three main types of die casting molds: single-cavity dies, multi-cavity dies, and family molds. Single-cavity dies produce one part at a time and are commonly used for simple designs. Multi-cavity dies can produce multiple identical parts simultaneously, increasing production efficiency. Family molds produce multiple different parts in one cycle, ensuring balanced inventories of parts typically used together. The choice of mold type impacts the overall cost of the mold and production efficiency, with multi-cavity and family molds offering higher output rates and cost savings for high-volume manufacturing.
Zinc Part Advantages
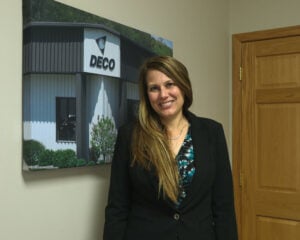
Michele Duwe
Michele Duwe is the Sales and Marketing Manager with Deco Products. She has eight plus years as a digital marketing manager and a decade of sales and marketing experience.