Deco Products was excited to recently be featured on The Manufacturing Experts Podcast hosted by Neal Rabogliatti. During this interview Dave Magner, our Sales and Marketing Director discussed what is zinc alloy fluidity. Let’s dive in and unravel the intricacies of zinc alloy fluidity.
What is the Zinc Alloy used in Die Casting
The process of zinc diecasting, it’s all about the right chemistry. The right recipe of this metal alloy, which includes different components for zinc.
The number one component within the zinc alloy is zinc itself, with aluminum coming in second. And the chemistry is so, so important. It really impacts the different characteristics of the alloy and really lends itself well to what is important to the designer.
And so, the zinc diecasting process is all about melting that material down. Then using a two-half mold so that you shoot this molten zinc in and able to achieve the right geometry. Which would relate to really the right functionality of the part. Therefore, the type of material is so, so key in that process.
What about the zinc alloy is important when considering the part design?
There are different materials that can be melted down and shot into a mold plastic, aluminum, magnesium.
But zinc has its fit for certain applications. An important aspect to zinc is to understand the intricate, complicated features of the part itself.
Zinc has great dimensional stability. A big part of that is how it melts and how it fits into the mold and then ultimately cooled. And understanding really what your base material is, whether it’s plastic or zinc, is important in part design.
What is Zinc Alloy Fluidity and Why is it Important?
Zinc, rather than some other materials, is very fluid. When it melts, it’s almost like water and it’s all about the viscosity of the material. Where other materials might be more syrupy, the nature of zinc alloy, when melted, is very fluid.
Ultimately, it flows very well up until the point it’s cooled. When it is cooled, it can get into certain areas of the mold that can be very detailed.
It might be a closer tolerance that you need. It may be a small feature that other materials just couldn’t achieve. With zinc alloy fluidity the chemistry of zinc and how it’s processed is so key.
Can the characteristics of a zinc alloy fluidity impact the part cost and other financial aspects of the project?
Yes, zinc alloy fluidity impacts the cost in a couple of ways. The fluidity aspect can be strategically used so that thin walls can be created, because zinc is a fairly strong material rather than a really thick wall.
With design strategy, and preliminary Finite Element Analysis (FEA) flow analysis, you can determine how to make that zinc wall thinner than another material. That wall thickness can be less and ultimately material saved and cost saved.
Another aspect about zinc alloy fluidity and some of the aspects of zinc and that it can be dimensionally, very stable. With other materials those features might require a secondary operation.
You may not be able to hold those tolerances or create features in other materials. In zinc you can, thus avoiding all that post processing cost. Those are a couple of elements where zinc and the fluidity of zinc really can help out with the cost impact.
Part Material Selection Impacts Part Cost, This Could Be Key to the Success of the Project?
Absolutely. It is important because weight and material is a big factor in one’s cost. If you can design that material in a way that it’s thinner and less materials used.
You’re going to achieve a better cost basis on that product.
Tune into the podcast for the complete interview.
Additional answers to questions asked in the podcast are:
- Designing with zinc alloy can impact both the end user and even impact the environment. Really?
- Are there particular industries or applications where zinc fluidity are more important than other areas? In other words, are there industries that this is more of a factor than others?
- What would you say would be the main challenges when you’re working with zinc alloy fluidity? And does that affect the manufacturing process or the end product?
- It sounds like there’s a lot of upfront work in the design to get everything to collaborate, to work together. If somebody is looking to design in zinc is that something that they design, and they bring to you? Or do you collaborate with the engineers to kind of bring it all to fruition?
About The Manufacturing Experts Podcast: An advertising free community for manufacturers looking for information, expertise and what’s new in the world of manufacturing. We cover a wide range of topics from digital marketing for manufacturing to innovations and explanation of manufacturing processes. We let the experts explain through informative and entertaining episodes. Our hosts have over 20+ years in manufacturing and have searched for subject matter experts to share their insights with our audience.
Advantages of Zinc Die Casting
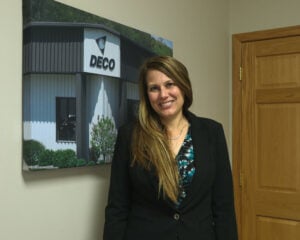
Michele Duwe
Michele Duwe is the Sales and Marketing Manager with Deco Products. She has eight plus years as a digital marketing manager and over a decade of sales and marketing experience.