At Deco Products, we specialize in zinc die casting. Instead of integrating multiple capabilities and materials like zinc, aluminum, magnesium, and plastic, Deco Products specializes in processing castings with alloys with higher percentages of zinc metal. This focus allows us to provide the innovative, practical, and best zinc die cast support and solutions. While we primarily provide raw castings, certain designs may require additional zinc die casting value add process.
Here are some crucial processes offered by Deco Products:
- Vibratory Degating: Vibratory degating in zinc casting is an efficient removal method of the gating systems where a machine vibrates and separates the function part from the excess material. The excess material includes the gating system with the sprue, runner, and gates that enable the flow of molten zinc into the mold cavity.
- Part Trimming: Part trimming is an essential process in die casting that involves removing excess material or flash from the cast parts.
- Tumbling: Tumbling involves subjecting the casted parts to a rotating barrel or vibratory machine, along with abrasive media, to remove burrs, smooth rough edges, and achieve a desired surface finish.
- Buffing: Buffing in zinc die casting involves using a polishing wheel or abrasive compounds to create a smooth, glossy, and reflective surface on the casted parts.
- CNC Machining: CNC machining is a precise and automated process of shaping, cutting, and drilling the cast parts using computer-controlled machines, resulting in high-accuracy and intricate details.
- Powder Coating: Powder coating applies a dry powder to the surface of the cast parts, which is then cured under heat to create a durable, uniform, and aesthetically appealing finish.
- Corrosion Protective Plating: Corrosion protective plating applies a thin layer of protective material, such as zinc chromate, or another corrosion-resistant coating, to the surface of the casted parts to enhance durability and resistance to various forms of corrosion.
- Decorative Plating: Decorative plating is the process of electroplating the cast parts with a layer of decorative metal, such as chrome, nickel, or brass, to enhance their visual appearance and provide an attractive and lustrous finish.
- Assembly: Assembly consists of joining or integrating multiple individual cast parts, along with other components if required, to create a complete and functional product or assembly.
- Kitting: Kitting in zinc die casting encompasses the organization and packaging of multiple casted parts and related components together as a kit, often with clear labeling and instructions, to facilitate easy identification, handling, and efficient assembly or installation processes.
Advantages of Zinc
Some advantages of zinc include stronger parts, thinner walls, faster production, tighter tolerances, less/no machining, longer tool life, fewer failures, better surface finishing, and design flexibility.
Zinc Die Casting Value Add Process
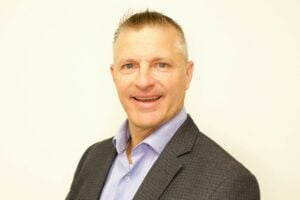
Dave Magner
Dave Magner is the Director of Sales and Marketing and has been with Deco Products since 2015. He has a +20 years of engineering experience in mechanical and electrical testing and design and zinc die casting, plastic injection molding, stamping, assembly, and automation processes.