Die casting molds play a crucial role in zinc manufacturing, producing complex and intricately designed zinc parts. Molds are created with hardened tool steel to endure the intense heat and pressure that arise during zinc casting.
Understanding Die Casting Molds
A die casting mold is a specialized tool used to produce high-precision zinc parts. A Deco Die Cast Operator injects molten zinc into two halves or dies of the die cast mold under high pressure.
Deco works with local tool shops to create die cast molds from hardened steel, making them extremely durable. The intricate design and size of die casting molds can be surprising to people who are not familiar with the process. These tools are heavy and complex, but the design, fabrication, and set up of these molds allow for low cost and consistent production for difficult parts.
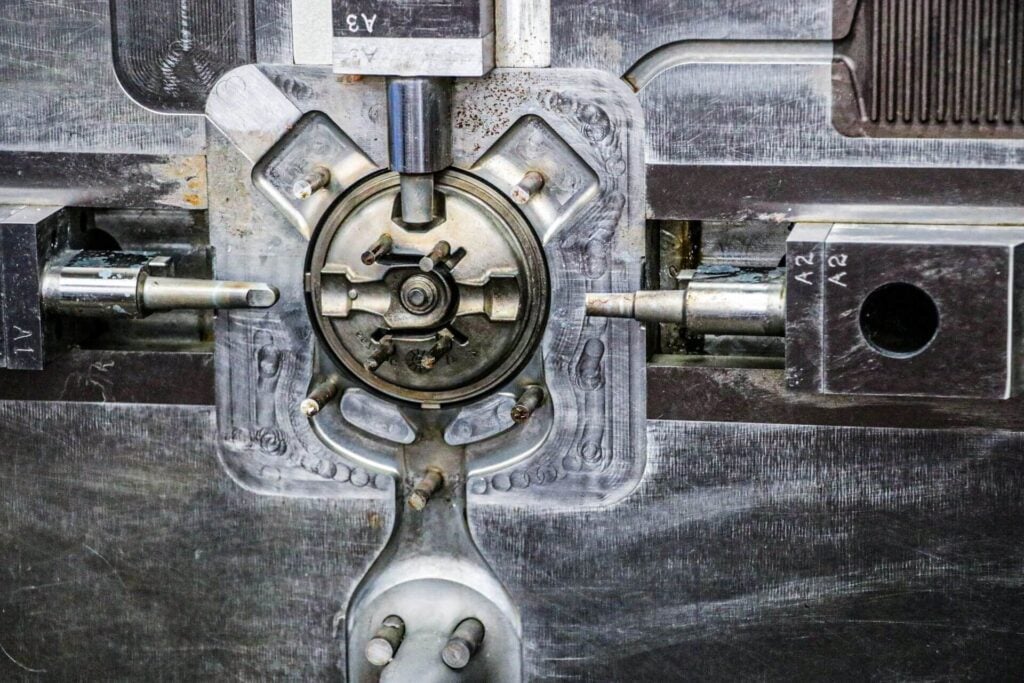
Critical Factors for Ensuring Die Cast Mold Quality
A quality die cast mold is a fundamental element in the die casting process. At Deco Products, we prioritize “up front” design considerations so that engineering decisions and tradeoffs can be addressed and balanced earlier to optimize future processes.
Our goal is to consistently produce high-precision zinc parts while minimizing defects. This approach ensures more stress-free product launches with long-term reliability through the entire life cycle of the part.
These are a few of the critical factors that we consider during the mold design process.
Material Selection: The choice of material for the mold is critical. High-quality die cast molds are typically made from hardened steel. Steel offers the necessary strength and durability to withstand the high pressures and temperatures involved in the die casting process.
Precision and Tolerance: A quality die cast mold must be precisely engineered to meet the required tolerances and specifications for the parts it produces. Precision is crucial for ensuring consistent and accurate part dimensions. Deco Engineers utilize Mold Flow Analysis Software to anticipate potential issues that may arise during the casting process. Read more about Mold Flow Analysis.
Surface Finish: The surface finish of the mold can impact the final appearance and quality of the zinc cast parts. A smooth and well-finished mold surface helps in achieving a polished and defect-free part.
Cooling System: Effective cooling is essential to solidify the molten metal quickly and prevent defects such as porosity. Quality molds are designed with efficient cooling channels to control temperature and ensure even cooling.
Venting: Proper venting within the mold is necessary to allow gases to escape as the molten metal fills the cavity. Inadequate venting can lead to defects like gas porosity or trapped air bubbles in the final part.
Ejector System: The ejector system should be designed for smooth and consistent part removal after the casting process. It should minimize the risk of part distortion or damage during ejection
Durability: A quality mold should be able to withstand the stresses of repeated use without excessive wear or deformation. It should have a long lifespan to ensure cost-effectiveness.
Ease of Maintenance: Regular maintenance is essential to keep the mold in optimal condition. Quality molds are designed with ease of maintenance in mind, making it simpler to clean, inspect, and replace components as needed.
Zinc Alloys: Die cast mold intended for use with specific zinc alloys should be designed to withstand the unique properties and characteristics of those alloys, such as their melting temperature and fluidity.
Testing and Quality Control: Mold setup and resulting production will have a plan for quality called a “control plan”. This identifies features of the part that should be monitored. These features are often important for design functionality and/or characteristics that are more sensitive to operational variation so that important characteristics are monitored to ensure ongoing part consistency and quality.
Cost-Effectiveness: While quality is paramount, it is also essential to consider the cost-effectiveness of the mold in terms of its initial cost, maintenance, and the overall value it brings to production.
Deco Products: Your Zinc Die Cast Manufacturing Authority
As mentioned earlier, the die cast mold is critical for the zinc alloy casting process. Deco Products recognizes the critical role of its design in achieving top-notch castings. Since 1960, Deco Products has been committed to designing, fabricating and maintaining die cast dies. Ensuring a smooth and efficient manufacturing process that yields high-quality zinc parts with unparalleled precision and consistency.
Just like any manufacturing procedure, success hinges on attention to detail and an unwavering dedication to continuous improvement. Deco Products sustains its leadership by remaining at the forefront of mold design and technological advancements. This unwavering commitment empowers us to consistently deliver the highest quality zinc alloy castings to our valued customers.
Conclusion
At Deco Products, we create high-precision zinc alloy metal parts and assemblies that are both high quality and cost-effective. We are particularly proud of our ability to use zinc alloys, which makes our products incredibly versatile. Our team of highly skilled engineers bring intricate designs and complex shapes to life, which is no easy feat! We believe our design process is a cut above the rest, and we are proud of the parts we cast for our customer partners.