Before designing your next part, we would like you to consider zinc alloys for your material selection. Zinc in castings offers many benefits including parts strength, finish and corrosion resistance.
Zinc in Die Castings Provide Strength and Ruggedness
When you consider the benefits of zinc, a multitude of benefits exist. In comparison to aluminum, zinc is stronger, and this can be evaluated in many ways.
The impact strength of zinc is far superior to all the other diecast alloys, especially compared to aluminum, making it stand out among other die-casting alloys.
Even when loading in more gradual with less impact energy zinc still performs well compared to many alloys of aluminum. Usually, 380 aluminum is the main alloy that we compare to zinc. In addition, zinc has a good shear strength and compressive strength.
To see more data of the various zinc alloys, see the below link
Zinc Provides Longer Tool Life
You may be wondering how does the tool life of zinc compare to other metals? Another key benefit of zinc in casting from other materials is its lower abrasiveness and lower melting temperature.
Specifically, compared to that of aluminum, zinc alloy are less abrasive this allows for a better bearing surfaced when solidified, but also less tool steel erosion resulting in much better tool life.
Additionally, aluminum’s melting temperature is around 1,200 degrees Fahrenheit.
With zinc, our preheat is up to 780 to 800 degrees Fahrenheit with a melting temperature right around 722—although it does vary a bit depending on the alloy. The lower melting temperatures provides less thermal stress contributed to less mold erosion and improved performance of features of the tools such as slides and ejection mechanisms.
With less erosion, zinc allows for a longer die life—typically yielding about a million shots, and in rare cases, even exceeding three to four million shots. A similar aluminum mold might only get 10% of the same life resulting in a significant increase in tooling cost production variability of the life of the product.
Zinc Alloy’s Ability to Cast into Intricate and Fine Detailed Parts
Zinc’s high fluidity enables the casting of intricate and fine detailed parts. Therefore, making it an ideal material for precise and complex shapes.
You’re able to fill out fine details with zinc die castings, like forming of threads and other small details.
However, it is important to note that the fluidity of zinc also poses the challenge of flash.
Zinc Alloy’s Impact on the Final Product
Zinc’s ability to achieve a smooth surface finish greatly impacts the aesthetics and functionality of the final products.
Zinc is one of the better alloys for applying finishes, such as power coating or plating.

Zinc Corrosion Resistance
Zinc alloys are naturally corrosion resistant. If you leave zinc outside, it doesn’t “rust” as there is very little iron in its chemistry. Rather zinc alloys can provide some discoloration but will perform better than iron-based metals like steel. Then further finishes can be applied for even better visual appearance and corrosion protection.
In Conclusion
Understanding the unique material quality of zinc in castings offers many benefits including part strength, finish, and corrosion resistance.
In addition, an advantage of zinc is the low abrasiveness, increasing tool life greatly. In general, getting about a million shots from dies made from Supreme H13 Alloy for the die steel.
With the high fluidity of zinc alloys, it flows like water. Giving zinc the ability to achieve intricate details, like forming of threads and other small details.
Zinc is one of the easiest alloys to put any type of decorative plating or power coat. Making zinc a preferred material for die casting in a wide range of engineering applications.
As the demand for high-quality and durable components continues to grow, understanding the benefits of zinc in die casting becomes increasingly crucial for engineering professionals and manufacturers alike.
What At Different Zinc Alloys?
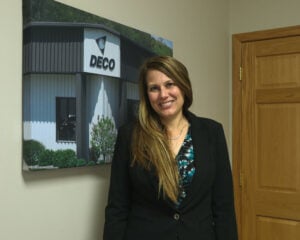
Michele Duwe
Michele Duwe is the Sales and Marketing Manager with Deco Products. She has eight plus years as a digital marketing manager and over a decade of sales and marketing experience.