Die casting is a widely used manufacturing process that involves the creation of complex zinc parts. The injection of molten metal into a metal mold creates a die cast zinc part. One important consideration in die casting is the placement of the parting line on the resulting part. The parting line, also known as a parting surface, is important for the tool design and to ensure proper quality and function of the part.
What is a Parting Surface?
First, we must look at how we create the diecasting. The parting line of a die casting refers to area of the part that aligns with the split line on a metal mold. As the 2 halves of the mold sperate the resulting split line enables the extraction of the cast part. So, it is important to understand that parting surfaces on the die casting are necessary as the mold halves are separated for part extraction.
The Design Process
Die cast engineers and designers need to consider many factors while deciding on the details that are involved in the die cast design process. One of the very important factors involved in the process is the cast part geometry and its relationship to the parting line placement. Designing an effective parting surface involves a careful examination of the part’s periphery to establish where to split the metal die to effectively release the part. This split will define which die half will become the ejector and cover mold halves. This process involves integrating elevation changes and core slides to accommodate varying geometries.
The finished product will exhibit a visible line around the perimeter. The line is exactly where the metal die elements come together to create the casting. This line is referred to as the parting line and holds the importance of determining how the remainder of the part will be designed.
Additionally, we introduce a slight angle, usually between three to ten degrees. This prevents shearing when the mold closes.

Minimizing Flash and Cost
Flash is an undesired excess thin material that forms along the parting surface. The high fluidity of zinc is a blessing and a curse. This fluidity allows for the ability to create vary complex geometry by flowing into small tight thin locations. Fluidity is a determinant when trying to seal desired locations.
A flat split line is desirable to reduce flash and can enhance the part’s aesthetics. Simultaneously, it can also diminish the necessity for extra operations, such as hand filing and/or trimming, leading to cost reductions.
Achieving flash reduction involves identifying casting features that, with slight modifications, could achieve a flat parting line and/or simplify elevation changes. A couple of examples of these features are recommending reduced corner breakers, altering slide core geometry, undercuts, and draft directional changes.
Parting location can also be very important when considering the optimal metal flow through the casting. Part corners and contours will affect the flow and can affect the casting aesthetics.
Considerations for Step Parting Lines
In certain cases, step parting lines are necessary to accommodate complex geometries with varying elevations. However, step parting lines increases the potential for flash formation.
Designers must carefully analyze the stepped areas keeping a visual for thin material conditions and undercuts within the steel mold. They strive to keep the design as simple as possible to minimize flash. While trim dies can aid in flash removal, they may not be completely effective because the draft on the casting. Therefore, minimizing the complexity of the parting surface remains crucial.
Parting Line Design and Production Efficiency
Efficient parting line design plays a vital role in the overall production process. A well-designed parting line ensures smooth mold opening and closing, reducing cycle times, and enhancing productivity. Additionally, it facilitates the proper ejection of the part, preventing damage and ensuring dimensional accuracy.
Conclusion:
Parting lines are a fundamental aspect of the die-casting process. They enable the extraction of cast parts from the mold. Additionally, they play a significant role in minimizing defects and production costs.
By strategically designing parting lines, considering part function and aiming for simplicity, manufacturers can achieve high-quality die-cast parts for longer life cycles. Understanding the nuances of parting line design empowers designers and engineers to optimize the die-casting process. This empowerment leads to the delivery of exceptional products.
Design and Engineering at Deco Products
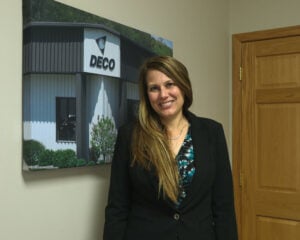
Michele Duwe
Michele Duwe is the Sales and Marketing Manager with Deco Products. She has eight plus years as a digital marketing manager and over a decade of sales and marketing experience.