Designing zinc parts can be a complicated process. There are many factors to consider, including the part’s function, the materials being used, and the manufacturing process.
As such, it’s essential to have a solid understanding of the best practices and techniques for designing zinc parts. We will explore valuable insights for zinc part design.
Additionally, we will explore some effective design techniques and best practices that can maximize the performance of your zinc parts. These include utilizing simulation tools, optimizing geometry, and ensuring proper surface finishing.
Considerations for Designing Zinc Parts
When designing zinc parts, there are several important considerations to keep in mind.
Firstly, it is important to consider the specific application of the part and how it will be used. This will help determine the optimal shape, size, and strength required for the part. The material properties of zinc, such as its strength and corrosion resistance, must also be considered in the design process.
Additionally, the manufacturing process must be taken into account to ensure that the part can be efficiently, and cost effectively produced. Both efficiency and effectiveness are considered during the launch of the product and also for the entire life of the product.
Designing for manufacturing is important for best results for initial part and tooling implementation, but also for minimizing quality issues and increasing tool life for best long term results.
Finally, it is important to consider any environmental factors that may affect the performance of the part, such as exposure to harsh weather conditions or corrosive substances. With this said, surface finishing techniques should be carefully considered, with a focus on achieving the desired aesthetic and functional properties. By carefully considering these factors, a designer can create zinc parts that are both effective and reliable in their intended applications.
Techniques for Designing Zinc Parts
When it comes to designing zinc parts, there are several techniques that can be implemented to ensure optimal results.
One important strategy is to carefully consider the part’s function and the type of zinc alloy that will be most suited for the application. Deco Products uses common Zamak alloys, but also other alloys with special characteristics that can be used in hot chamber die casting.
During the design for manufacturability phase of a project Deco’s engineering team can help with customer projects. They can review the design and then perform mold flow simulations to further understand the optimal design and to avoid future problems like porosity and other casting defects.
Designers must also consider the various manufacturing processes that will be utilized, such as die casting and then other “value add” secondary or finishing operations.
Attention should be paid to the surface finish and any necessary coatings or treatments that will be required. By implementing these techniques, designers can create high-quality zinc parts that meet their intended function and performance requirements.
Conclusion
To sum up, designing zinc parts requires careful consideration and following best practices and techniques to achieve optimal results.
It is important to understand the material properties, manufacturing process, and design limitations to create parts that are functional, efficient, and cost effective.
Whether it’s creating complex geometries or simple shapes, designing zinc parts can provide a great alternative to other materials and offer a range of possibilities.
Zinc Alloys
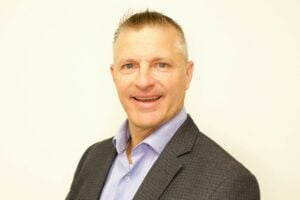
Dave Magner
Dave Magner is the Director of Sales and Marketing and has been with Deco Products since 2015. He has a +20 years of engineering experience in mechanical and electrical testing and design and zinc die casting, plastic injection molding, stamping, assembly, and automation processes.