Die casting is a manufacturing process that involves injecting molten metal into molds to produce a wide range of products. Why use zinc for die casting, not all materials are suitable for die cast products, and zinc alloys are often an optimal choice.
Zinc alloys are a popular choice among manufacturers with products with a high production rate, dimensional stability, finishing options and cost-effectiveness.
Why Use Zinc for Die Casting?
Zinc is a highly fluid material, making it an ideal choice for hot chamber die casting. The zinc die casting process involves melting zinc alloy and injecting it into a harden steel mold. This process utilizes high pressure to force the molten metal into the intricate cavities of the die to create exact features and complex part shape.
Because of their specific physical and mechanical properties zinc alloys have high fluidity.
Deco Products is a die caster that only uses high quality certify alloys that conform to exact chemistry requirements.
These alloys have lower melting temperature than cold chamber aluminum die casting alloys with but also high fluidity and strength.
The lower melting point allow for processing in hot chamber die cast equipment that can run at higher pressures and quicker rates resulting in higher precision, stronger thin wall die cast products.
Cost is optimized by eliminating or reducing secondary operations by casting near net shape parts.
Also, tool life can be much longer for zinc alloys to help ensure a lower total life-span cost of part’s design life.
Zinc alloys have optimal design characteristics (high strength, hardness and precision)
Zinc alloys, also to their precise chemistry, have desirable mechanical properties. They are highly regarded for their impressive strength and hardness, making them an ideal material for part design in zinc die casting alloys.
Deco Products casts many types of alloys depending on specific design parameters.
These alloys are known for their ability to withstand heavy loads and high stress environments, while retaining their structural integrity.
The high strength and hardness of zinc alloys is because of the addition of other metals such as copper, aluminum, and magnesium. This results in a material that is not only strong and durable, but also lightweight and easy to work with. Overall, zinc alloys are a reliable and versatile material that is widely used in numerous industries.
Also, as mentioned above, zinc alloys include the cost benefits of faster production times and reduced waste with design efficiencies. Lastly, zinc alloys, are less abrasive when used in die casting and thus provide longer mold life. Zinc die casting tools can have a significantly longer die life than other materials—and typically 10 times longer than other materials such as aluminum. This provides much cost savings and higher quality over the life cycle of a part.
In summary, zinc’s unique properties and characteristics make it an excellent choice for die casting, and it will undoubtedly continue to play a critical role in many industries. It is also cost-effective and readily available, making it a popular choice for manufacturers. Additionally, zinc’s ability to be recycled and reused multiple times makes it an environmentally friendly option. As technology continues to advance, we can expect zinc die-casting to remain a vital component in the production of high-quality products.
Discover Deco Products
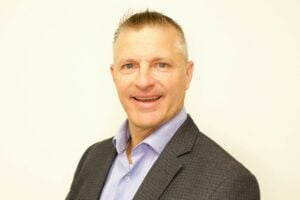
Dave Magner
Dave Magner is the Director of Sales and Marketing and has been with Deco Products since 2015. He has a +20 years of engineering experience in mechanical and electrical testing and design and zinc die casting, plastic injection molding, stamping, assembly, and automation processes.